Essa semana continuamos com a sequência de posts abordando o processo de Strip Planking em Espuma PVC, desenvolvido pelo departamento de engenharia da Barracuda Advanced Composites. Depois de passar uma visão geral do método, vamos falar agora especificamente do corte e posicionamento das cavernas.
A construção e posicionamento do picadeiro têm a fama de serem uma das etapas mais complicadas do processo. O picadeiro é a base da construção e deve ser forte o suficiente para suportar o peso das cavernas e do laminado do casco sem apresentar empeno e deformação. Pode ser construído de madeira, aço ou alumínio entretanto a madeira é provavelmente o material mais simples de se utilizar e oferece um bom desempenho quando são utilizados perfis de 6”x3” de madeira de boa qualidade, sem empenos, sem nós e sem umidade.
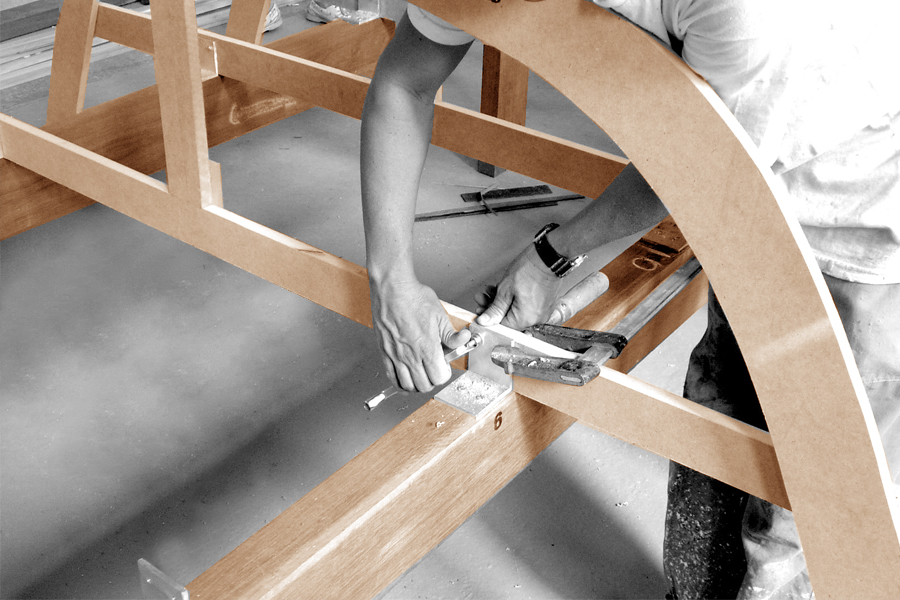
Como regra prática, pode-se adotar que o picadeiro deve ter uma largura equivalente a 60% da boca máxima do barco. Sua altura vai evitar que as etapas posteriores do projeto sejam executadas em posições desconfortáveis que podem até comprometer a estética do barco. Em geral, a altura da linha de borda deve ter pelo menos 300 mm sobre o piso do estaleiro para facilitar o trabalho posterior de montagem das ripas, laminação e acabamento. O comprimento do picadeiro deve ser um pouco maior do que o do barco, permitindo que seja possível trabalhar no espelho de popa.
Depois de construir e posicionar o picadeiro, é hora de posicionar as cavernas. Hoje em dia, é muito comum que o projetista envie as seções do barco em padrão digital e as seções sejam cortadas por controle numérico (CNC) e o processo pode ser finalizado em algumas horas. No entanto, é importante que alguns detalhes sejam destacados.
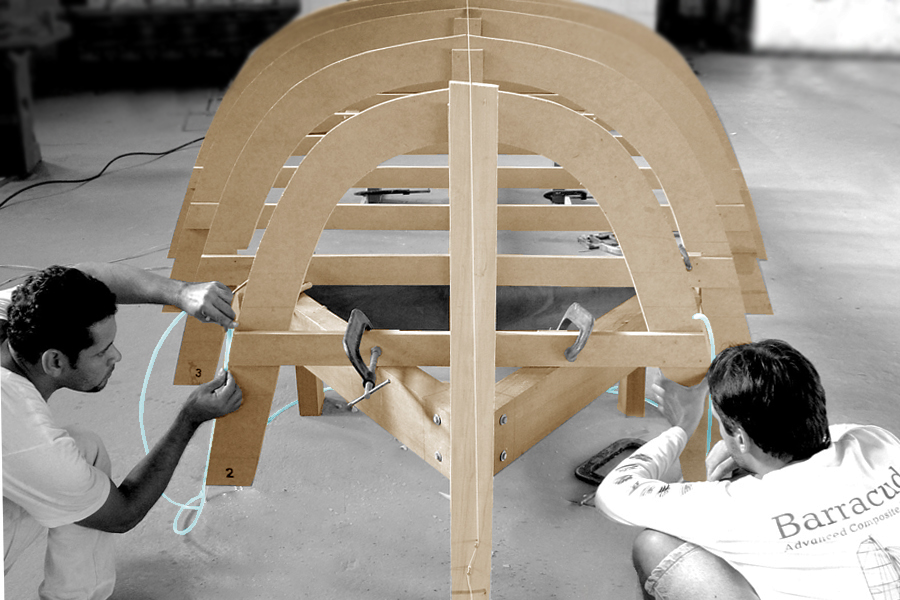
Em primeiro lugar, as dimensões da caverna devem considerar o desconto do ripamento de Divinycell e a laminação. Para plugs que necessitam de ripas intermediárias para montagem de alguma curvatura ou diferença de espessuras, os encaixes já devem estar entalhados nas cavernas e é papel do construtor inserir isso no desenho de corte.
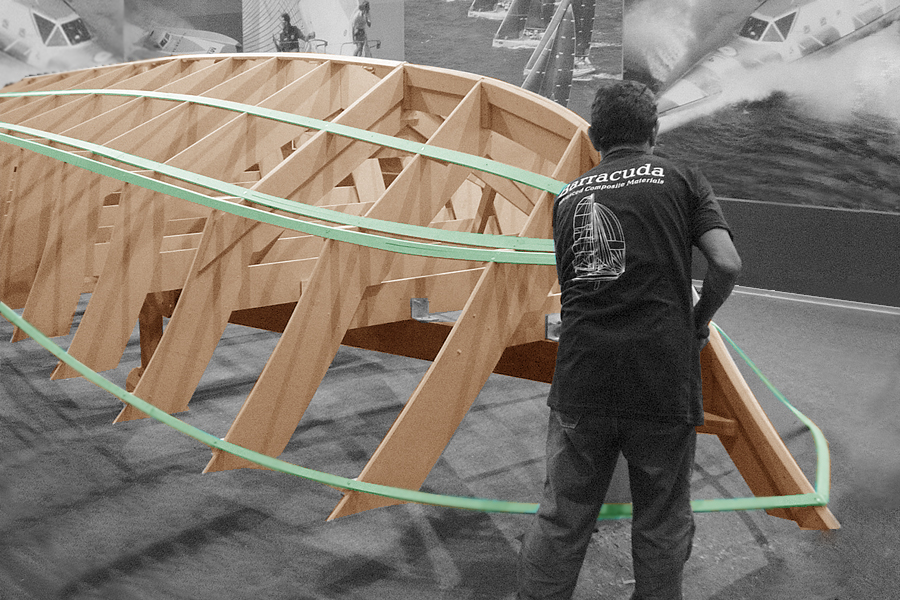
Uma boa opção de materiais para construção das cavernas são placas de MDF de pelo menos 15 mm de largura. Espessuras menores não vão suportar o peso sobre elas e as bordas tendem a abrir quando fixadas com parafusos e pregos. O corte em CNC permite que se façam furos de passagem que deixar as cavernas mais leves e fáceis de serem manuseadas.
Antes de posicionar as cavernas, as posições longitudinais devem ser marcadas no picadeiro com precisão. Um erro na posição das cavernas significa uma deformação no casco, portanto é muito importante que esse processo seja feito de forma precisa, com trena de fibra com comprimento suficiente para não haver emendas ao longo do comprimento do barco. Outra opção é utilizar um medidor ótico para garantir total precisão. Hoje em dia existem várias ferramentas auxiliares de posicionamento e nivelamento para que a montagem tenha 100% de precisão.
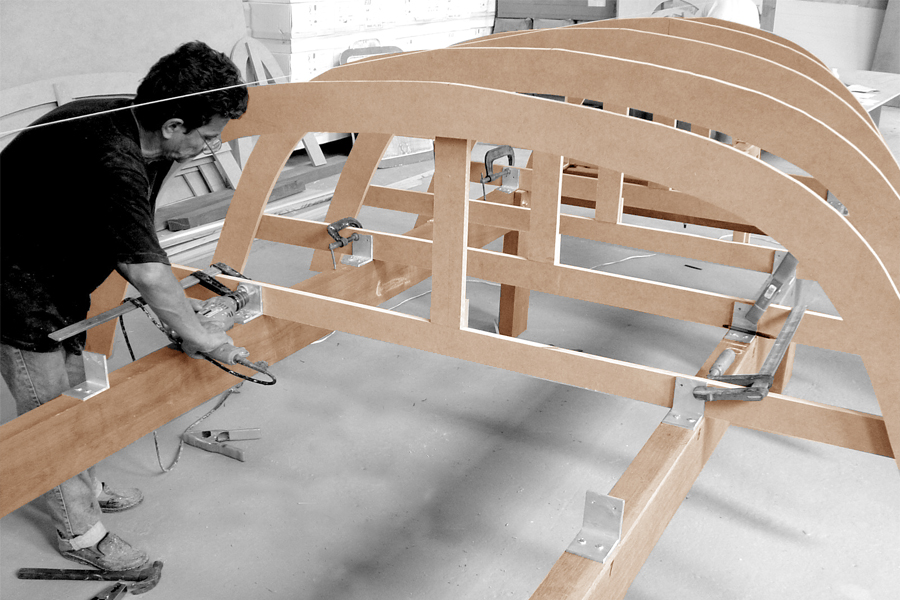
Assim que for colocada na posição, a caverna deve ser travada com auxílio de grampos e seu nível lateral deve ser verificado com linha, mangueira de nível ou mira a laser. A caverna deve ser fixada em sua posição apenas depois do seu ajuste no nível vertical, que normalmente começa no centro do barco.
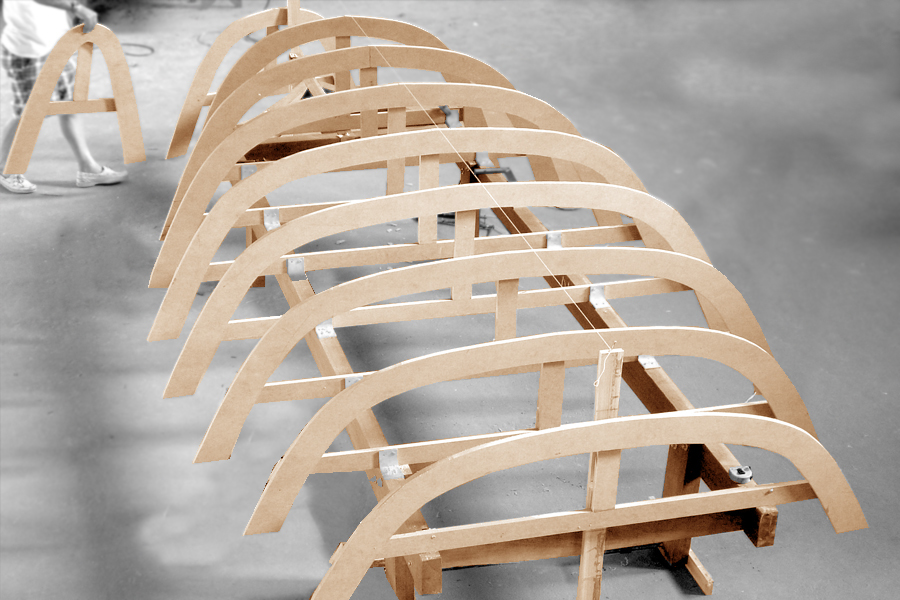
Outro ponto crucial é a colocação da roda de proa. Ela deve considerar o ângulo de fechamento das ripas de Divinycell e seu perfil deve descontar proporcionalmente esta angulação. Para quem tem familiaridade em ler um plano de linhas isto não será problema.
Clique aqui para acessar Strip Planking em Espuma de PVC – Parte 3
Clique aqui para acessar Strip Planking em Espuma de PVC – Parte 1