O processo Power Flex é uma maneira de utilizar a eficiência mecânica e produtiva do processo de infusão para a construção de barcos one-off em cascos com o formato multichine. Nos posts anteriores foram abordados os conceitos e as etapas de construção dos painéis k-lite e fabricação e montagem dos picadeiros e cavernas.
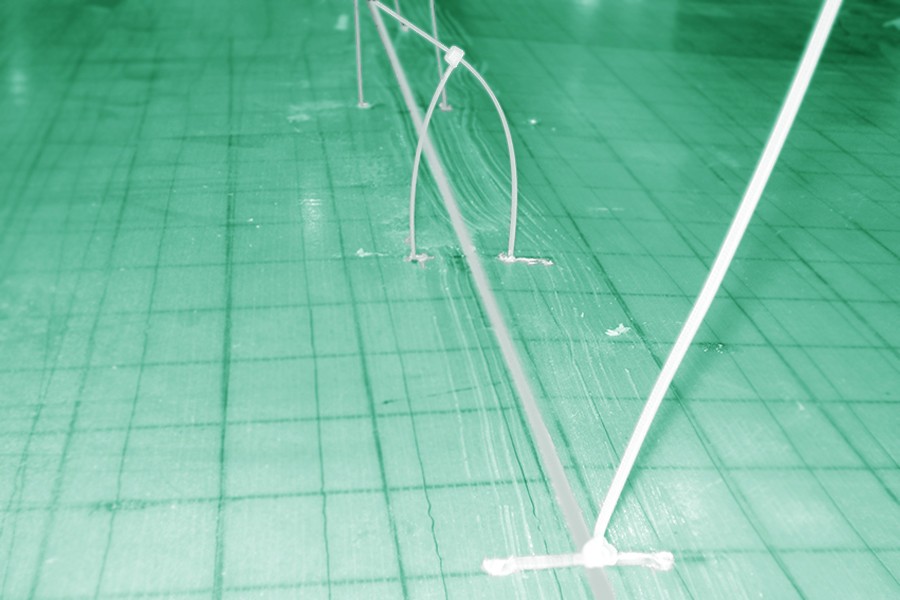
O que se segue é o processo de consolidação e acabamento do casco, realizado por meio do posicionamento dos painéis k-lite utilizando abraçadeiras de plástico. As linhas de colagem devem então serem preenchidas com adesivo de base epoxy e sílica e a integridade estrutural da embarcação é garantida a partir da laminação manual de tapes de fibra de vidro nessas linhas. Depois é a vez da etapa de acabamento, composta pela aplicação de massa no casco, seguida do primer e da pintura.
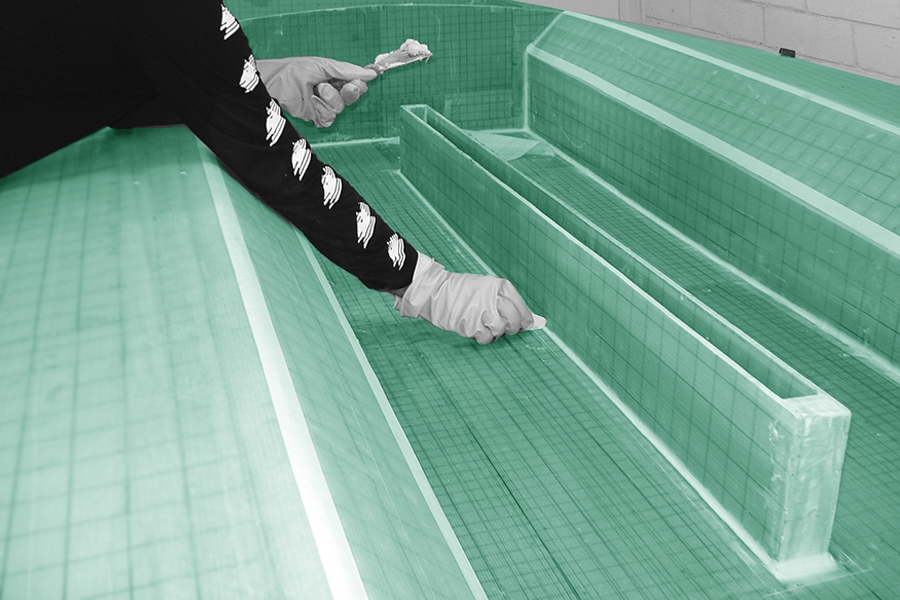
O primeiro passo para a montagem do casco é fazer uma série de furações com diâmetros de 3-4 mm nos painéis para que seja possível utilizar abraçadeiras plásticas para juntá-los na posição correta. A abraçadeira deve produzir pressão suficiente para manter os painéis juntos até a cura do adesivo e o espaçamento entre elas deve ser suficiente para evitar o empeno das arestas do painel.
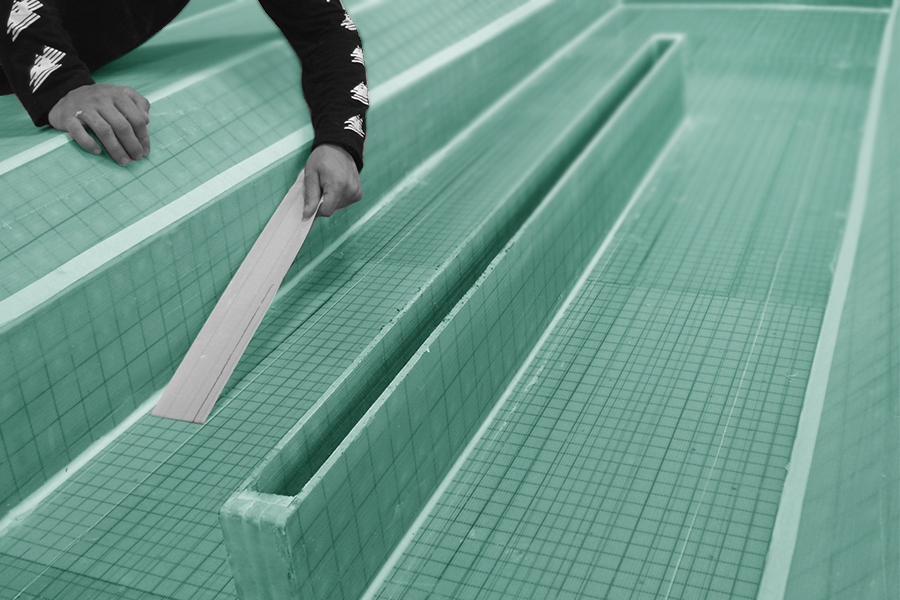
Quando as chapas estiverem posicionadas, as abraçadeiras devem ser retiradas para aplicação do adesivo sobre o topo das cavernas. Para garantir uma superfície livre de contaminação na etapa de aplicação de massa no casco, o peel ply dos painéis infundidos deve ser removido apenas na região onde o adesivo será aplicado. O adesivo utilizado deve ser à base de resina epoxy e sílica, para garantir a adesão entre os painéis e uma tixotropia que impeça o escorrimento entre as placas que, depois de receber o adesivo, devem ser posicionadas no local adequado e fixadas novas abraçadeiras de plástico.
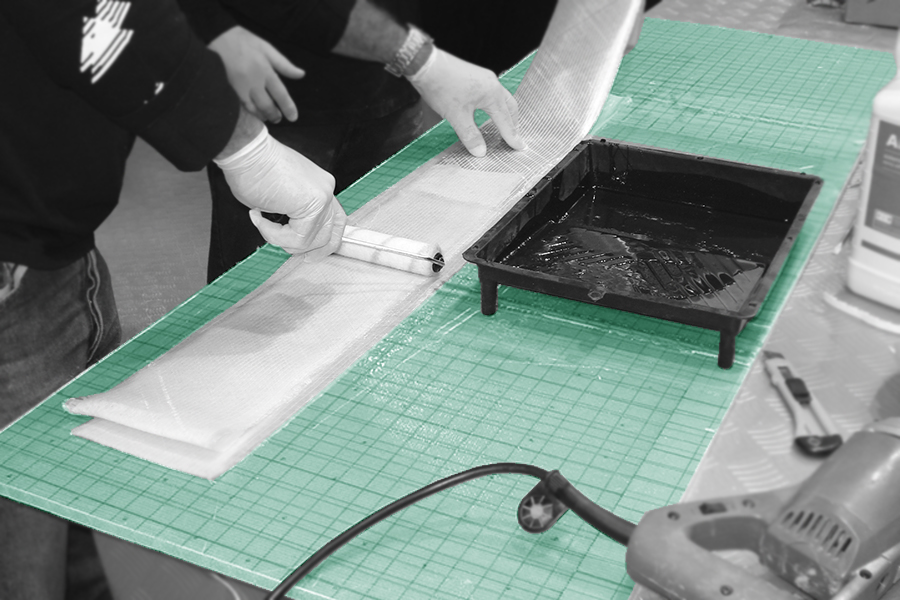
Após a cura completa do adesivo, é hora de realizar a laminação dos tapes na superfície externa do casco. Para começar, é preciso retirar as abraçadeiras plásticas e verificar se as linhas de colagem estão perfeitas. O peel ply na região das laminações deve ser retirado também e uma lixadeira de fita com lixa de ferro #40 ou #60 deve ser utilizada para preparar a superfície.
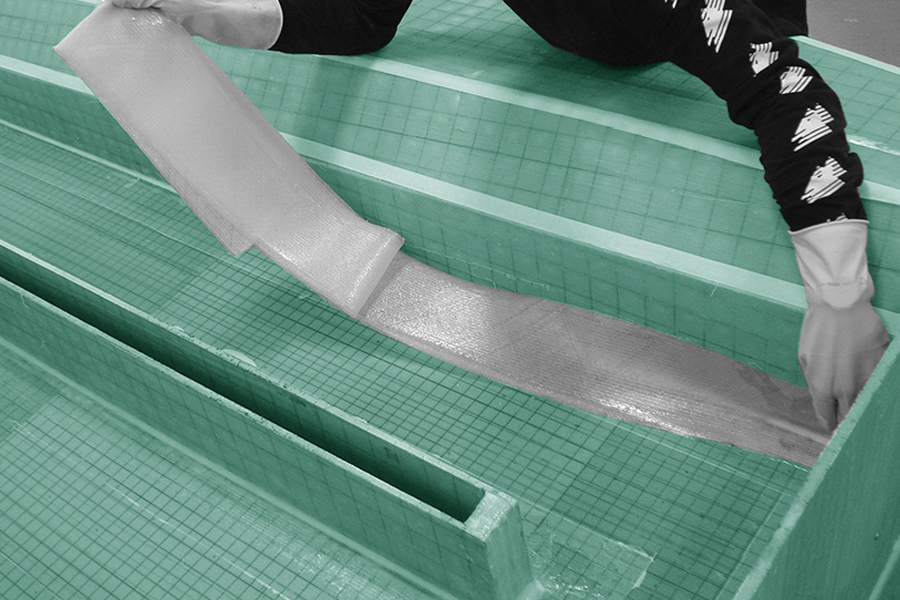
Os tapes devem ser contínuos e ter as bordas do tecido preparadas para evitar ressaltos. Em um barco pequeno, um tape de tecido biaxial [±45] com gramatura de 200-300 g/m² é a melhor opção em termos estruturais. A resina de colagem normalmente é à base de epoxy, de modo que se obtenha uma união sólida e resistente. Resinas poliéster podem ser utilizadas e apresentarão facilidade de manuseio, mas devem ser testadas para determinar sua compatibilidade com a resina utilizada nos painéis.
Antes de iniciar a laminação, é necessário aplicar na superfície uma pequena quantidade de pasta de resina catalisada com sílica, o que facilita a colocação dos tapes e evita que eles escorreguem sobre a superfície seca. Os tapes devem ser pré-impregnados sobre uma mesa de laminação antes de serem posicionado no casco e o peso de resina não pode ser superior a 50% do peso das fibras.
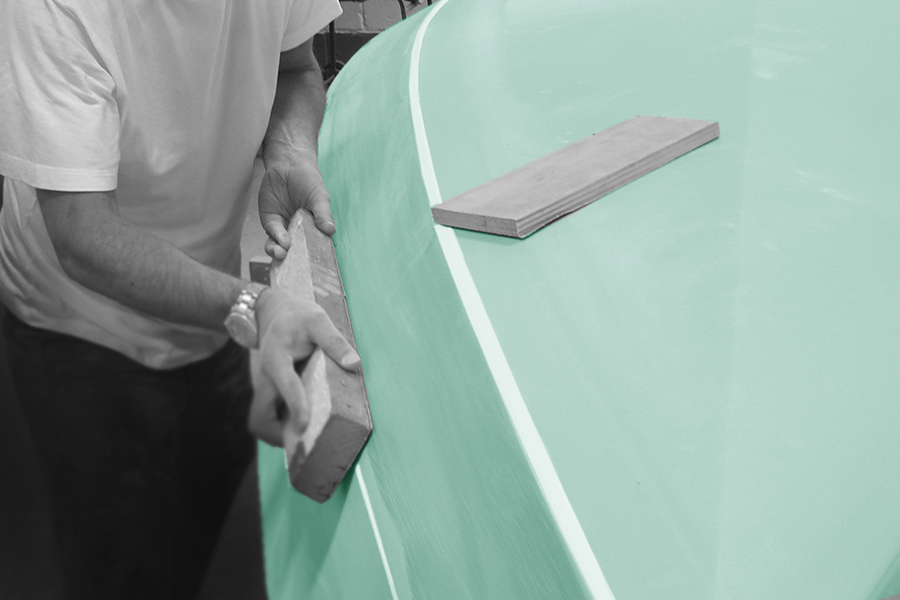
Depois de posicionado e acabado, uma tira de peel ply deve ser colocada em cima do tape para evitar que a resina fique exposta e para preparar a linha de colagem para receber o acabamento.
Após o posicionamento do peel ply em todas as linhas de colagem, é necessário virar o casco e realizar a laminação dos tapes na parte interna da mesma maneira. Só após a cura deles é que se inicia o acabamento com massa e tinta. É possível escolher entre massas de epoxy e de poliéster para o acabamento.
Seguindo a aplicação da massa, o casco deve ser preparado para receber o primer por meio do lixamento manual e contínuo de forma progressiva com lixas de ferro de #40, #60 e #80. Com o casco limpo e livre de resíduos, o primer deve ser aplicado em duas demãos cruzadas para garantir uma superfície uniforme e com brilho. Depois de sua cura, é necessário mais um lixamento do casco, dessa vez com lixas de ferro de #60 e #80 e então é possível realizar a pintura e acabamentos finais.
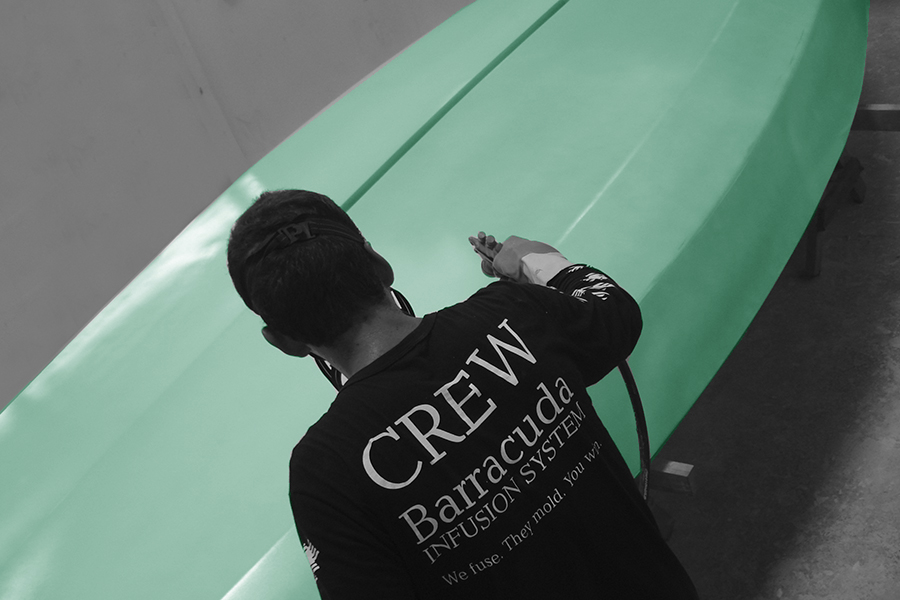
Para mais informações sobre o Power Flex, é possível adquirir o livro Técnica e Prática de Laminação em Composites, que descreve com detalhes o processo de construção do dingue Andorinha, projeto desenvolvido no escritório de Roberto “Cabinho” Barros, com fotos ilustrativas de todas as etapas.