O uso de vácuo para compactação de laminados aumenta o teor de fibras e diminui os vazios presentes nas estruturas, melhorando sua confiabilidade e propriedades mecânicas. Por essa razão, muitos estaleiros costumam adotar os métodos de laminação por vacum bagging ou infusão a vácuo.
Para construir embarcações utilizando esses métodos, é preciso mais do que apenas as fibras e resina. Para que aplicar pressão negativa no laminado é necessário utilizar uma classe de materiais chamada de consumíveis, que são utilizados durante o processo de compactação e descartados após a laminação.
Apesar de compartilharem muitos desses materiais, existem algumas diferenças entre o conjunto de consumíveis necessários para os processos de vacuum bag e de infusão a vácuo. O post dessa semana é dedicado a explorar os materiais necessários para o primeiro processo e, na próxima semana, serão caracterizados os materiais necessários para infusão a vácuo.
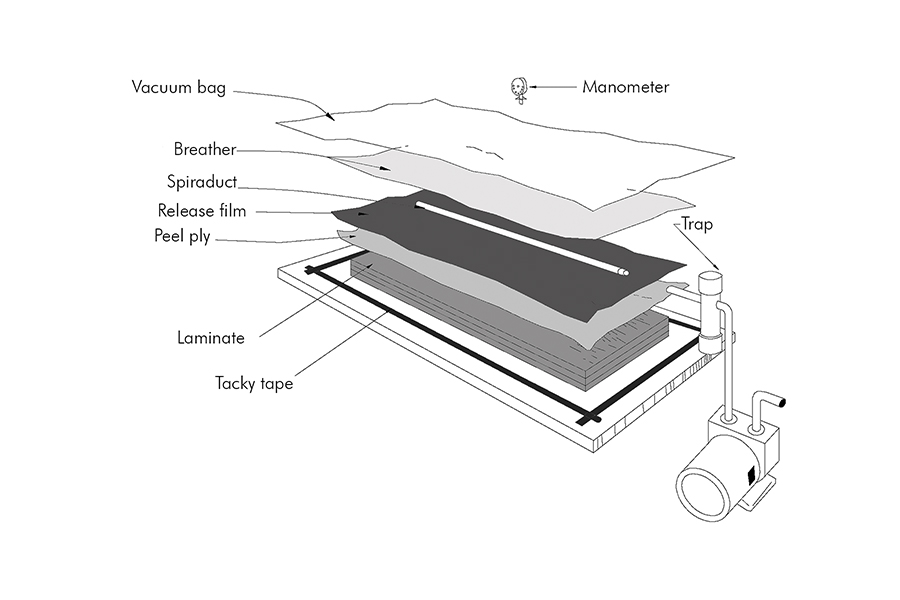
A primeira característica que o construtor deve ter em mente ao selecionar os materiais consumíveis é a temperatura que eles devem suportar, que depende da temperatura de pico que a resina alcança durante a cura exotérmica. Existes conjuntos de consumíveis que suportam temperaturas entre 100 e 200°C além daqueles desenvolvidos para pós-cura, que podem alcançar até 250°C. Em geral, os construtores de embarcações podem utilizar produtos que operam na faixa entre 120 e 180°C.
Ao preparar a laminação, o primeiro material que deve ser posicionado no molde é a tacky tape, uma fita adesiva emborrachada dupla face com 3 mm de espessura e 12 mm de largura. Sua função é fixar a bolsa de vácuo no perímetro molde sem permitir vazamentos, possibilitando a aplicação da pressão de vácuo sobre o laminado. A fita deve ser aplicada sobre uma superfície limpa e livre de desmoldante, além de ficar bem protegida durante todo o restante da montagem e laminação.
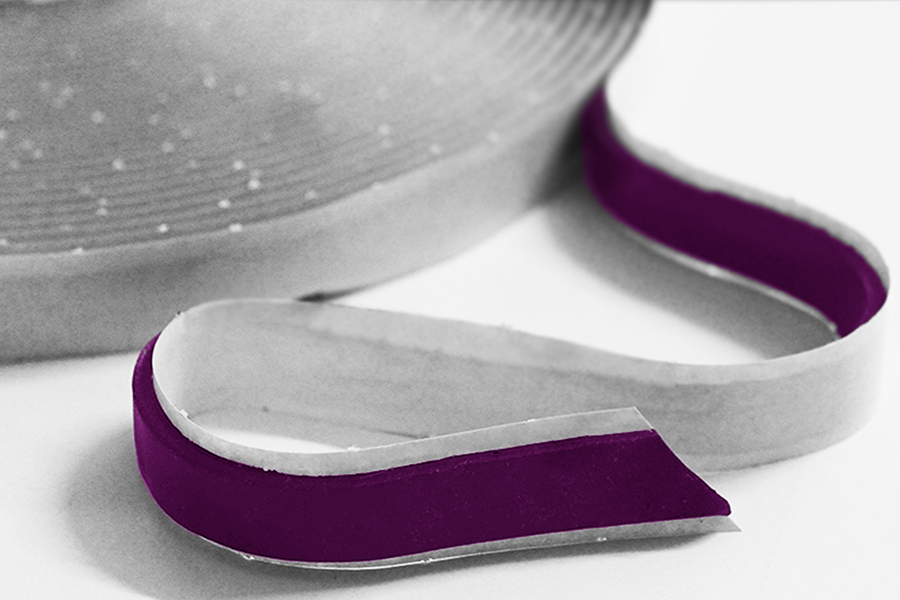
Depois da laminação das camadas de tecido de fibra, o próximo consumível a ser posicionado é o peel ply, um tecido desmoldante de fibras de poliamida ou poliéster. Suas principais funções são permitir a desmoldagem dos demais materiais consumíveis após a laminação e garantir que a face do que não está em contato com o molde tenha um acabamento superficial satisfatório.
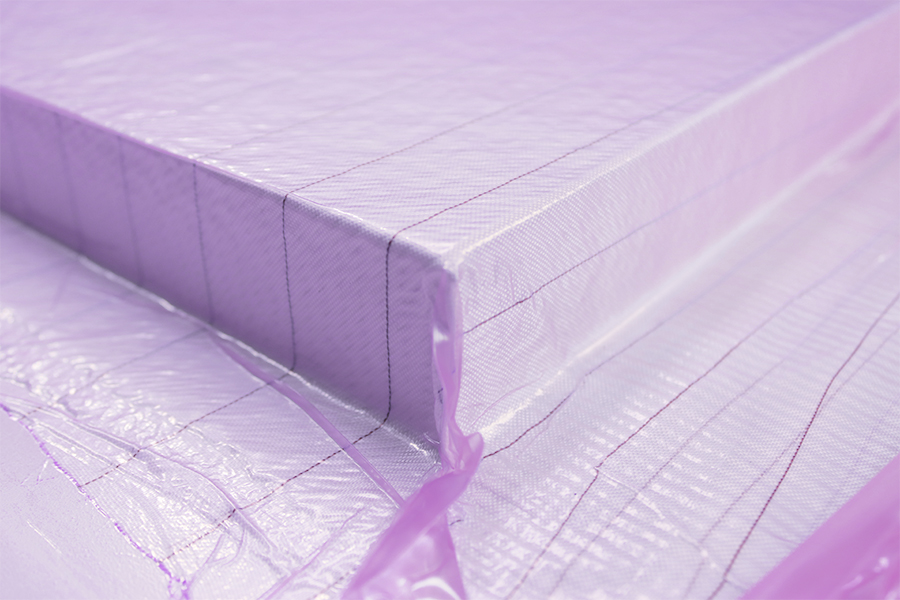
A maior parte dos tecidos peel ply possuem tracers vermelhos e pretos que contrastam com o laminado e ficam visíveis mesmo após a impregnação dos reforços, quando a parte branca do material se torna transparente.
Depois do peel ply, o constructor deve posicionar o filme perfurado, chamado também de release film, já que ele também facilita a desmoldagem do restante dos materiais consumíveis. Sua principal função no processo de vacuum bag é controlar a quantidade de resina que é retirada do laminado e absorvida pelo breather.
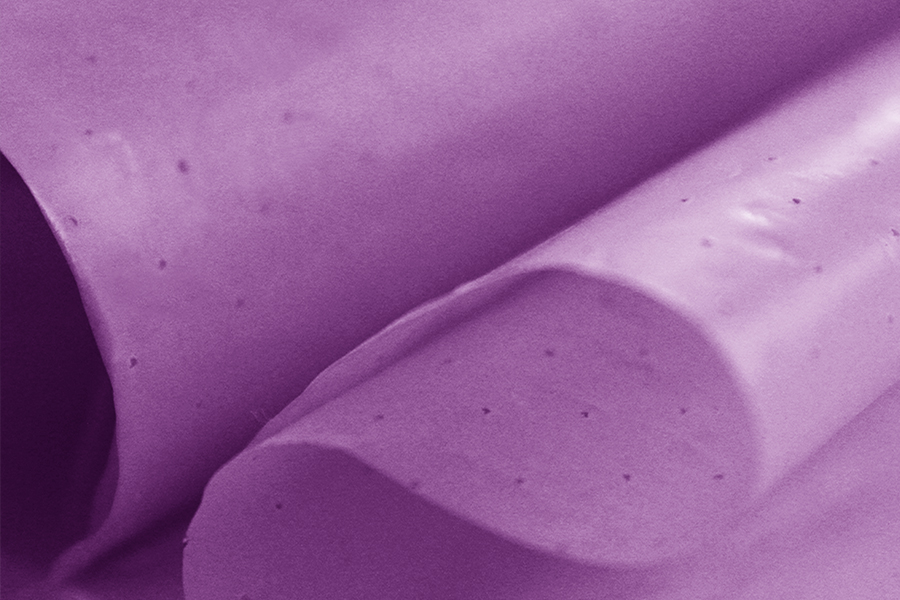
A área aberta é uma variável importante nesse tipo de material e deve ser definida a partir da quantidade de resina que o construtor deseja retirar do laminado, da viscosidade dessa resina e da intensidade do gradiente de pressão utilizado. Em geral, filmes perfurados com áreas abertas até 0,3% são utilizados para laminações por vacuum bag.
O breather, por sua vez, é uma material absorvente feito a partir de fibras de poliéster não tramadas. Ele é responsável por distribuir o vácuo por toda a superfície da peça e por absorver a resina que passa pelo filme perfurado. A homogeneidade desse material é de extrema importância porque variações em sua espessura significam uma variação na quantidade de resina retirada do laminado. Isso faz com que o teor de fibra seja diferente dependendo da região do estrutura, o que é indesejável.
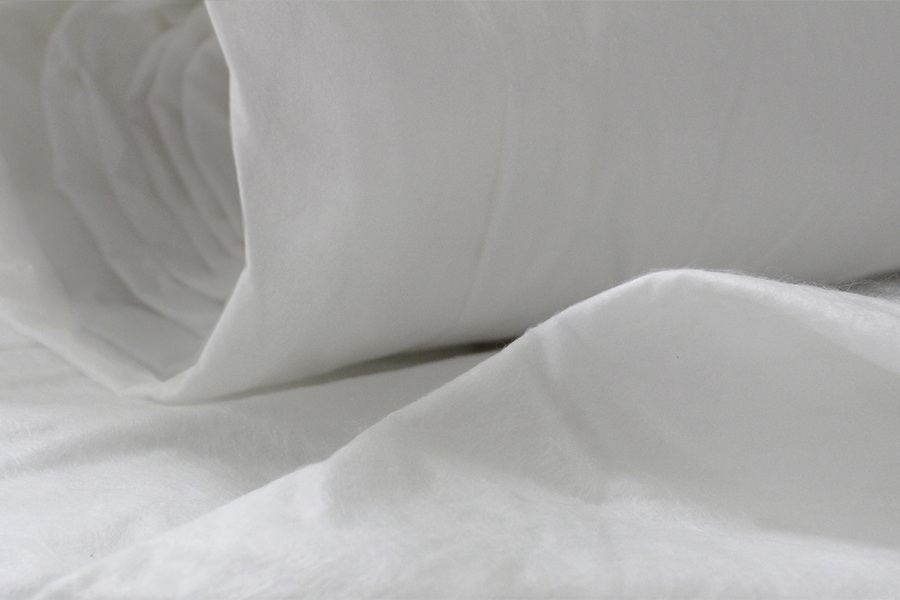
Entre o filme perfurado e o breather é interessante que seja posicionado um spiraduto de ½” ou ¾” que seja capaz de ajudar na distribuição da sucção causada pela bomba de vácuo. Ele deve estar ligado a uma conexão T que estará conectada a uma mangueira cristal e a um trap, onde a resina que deixar o laminado ficará armazenada. Todo esse conjunto de consumíveis deve estar preparado para suportar pressões negativas e não deve colapsar quando o vácuo for aplicado.
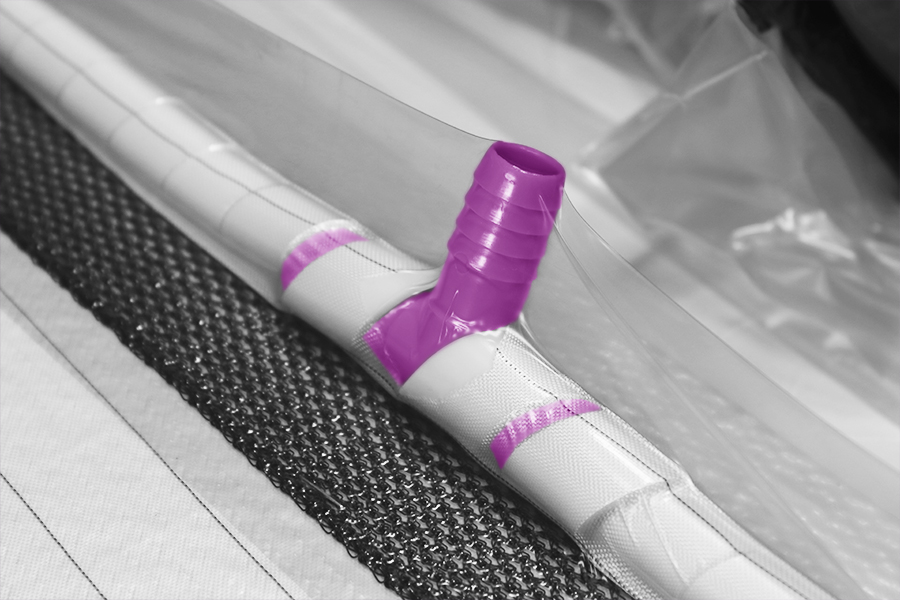
Por fim, acima de toda essa sequência de materiais, deve ser posicionada a bolsa de vácuo que é um filme de nylon com capacidade de elongação de 300% antes de se romper, além de uma resistência à tração de 55 MPa. Ele é fixado nas bordas do molde por meio da tacky tape de forma que não ocorra nenhum vazamento de ar, fenômeno que é monitorado assim como o explicado no post sobre Integridade do Molde.
O custo extra que o construtor tem para adquirir esses materiais é mais do que compensado pelo ganho de qualidade no laminado e economia de tempo de produção. Na próxima semana o post do blog abordará as particularidades dos consumíveis utilizados para realização da infusão a vácuo e mostrará como se montam as saídas de vácuo e entradas de resina.
Fernanda Santana disse:
Eu gostaria de construir uma peça o processo de vacuum bag, mas estou com dificuldades de encontrar uma resina poliéster que tenha mais do que 30 minutos de geltime. Não acredito que esse tempo seja suficiente para laminar a peça, posicionar todos os consumíveis e ainda aplicar o vácuo. Como posso proceder?
Barracuda Composites disse:
Olá, Fernanda
Por conta do mecanismo de cura desse tipo de resina, é muito difícil que seu gel time seja consideravelmente maior sem que as propriedades mecânicas sejam prejudicadas. Normalmente as laminações por vacuum bag utilizam resinas epoxy que possuem uma variedade de endurecedores que permitem um tempo de trabalho consideravelmente maior, mas também serão mais caras.
Se você quer aliar os benefício da compactação à vácuo com o baixo custo da resina poliéster, vale considerar mudar o processo construtivo para infusão à vácuo.
Sabrina Fernandes disse:
Como saber o pico exotérmica da resina utilizada para selecionar os materiais corretos?