O método de construção em strip planking em espuma PVC, desenvolvido pelo departamento de engenharia da Barracuda Advanced Composites, tem os mesmos fundamentos do método utilizando madeira, que foi um dos primeiros processos utilizados para construção amadora de barcos a vela e para a construção de modelos e moldes. Nas próximas semanas os posts do Blog de Manual de Construção de Barcos vão explorar esse método, começando aqui por uma visão geral que elucida todas as vantagens e etapas do processo, e depois abordando a confecção e posicionamento das cavernas e colocação das ripas de espuma.
Esse processo é ideal para construção de embarcações one-off com o mínimo de ferramentas possível e baixo investimento inicial. É mais indicado para barcos com grande parte de superfícies planas, mas é possível produzir superfícies com dupla curvatura. No método tradicional de strip planking, a madeira desempenha toda a função estrutural e as camadas de fibra aplicadas na parte externa do casco têm apenas função de proteção contra umidade. No strip planking em PVC, a espuma tem a mesma função estrutural de um material sandwich, provendo resistência à compressão e ao cisalhamento e garantindo um casco muito mais leve do que se tivesse sua estrutura construída em madeira.
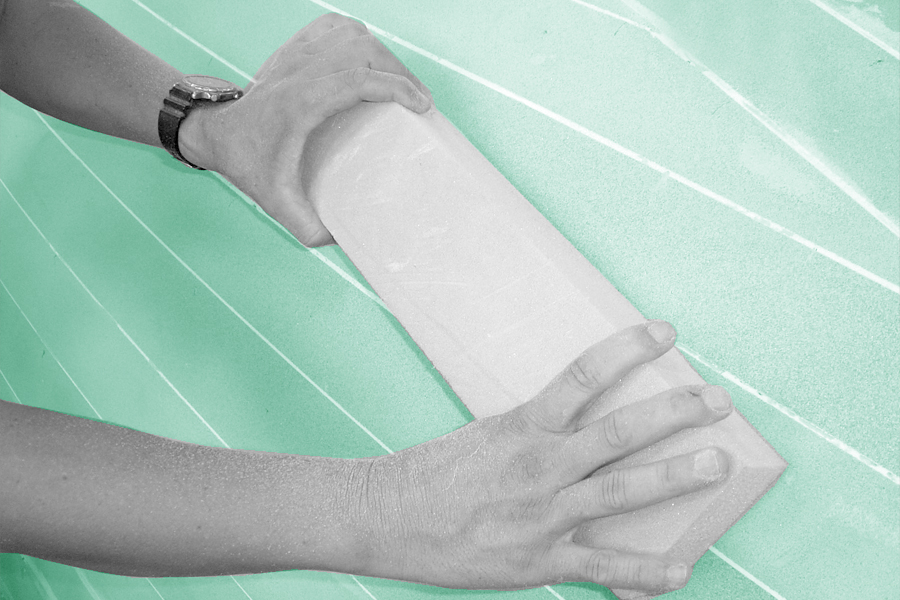
Além disso, barcos construídos com compostos sandwich tendem a não ter qualquer espécie de reforço longitudinal ou transversal, ou pelo menos não tanto quanto os usados em projetos de laminados sólidos e madeira. Barcos projetados e construídos em strip planking de madeira tendem ser dotados de uma série de cavernas transversais (90°) para compensar o uso de ripas longitudinais (0°) utilizadas no casco.
O processo de construção de strip planking em PVC começa com o posicionamento das cavernas, seguido do corte e posicionamento dos strips que são colados um nos outros com uma massa a base de resina poliéster. Depois disso, a superfície externa das espumas é preparada para laminação e acabamento antes do casco ser virado e laminação interna ser iniciada para a consolidação do painel sandwich.
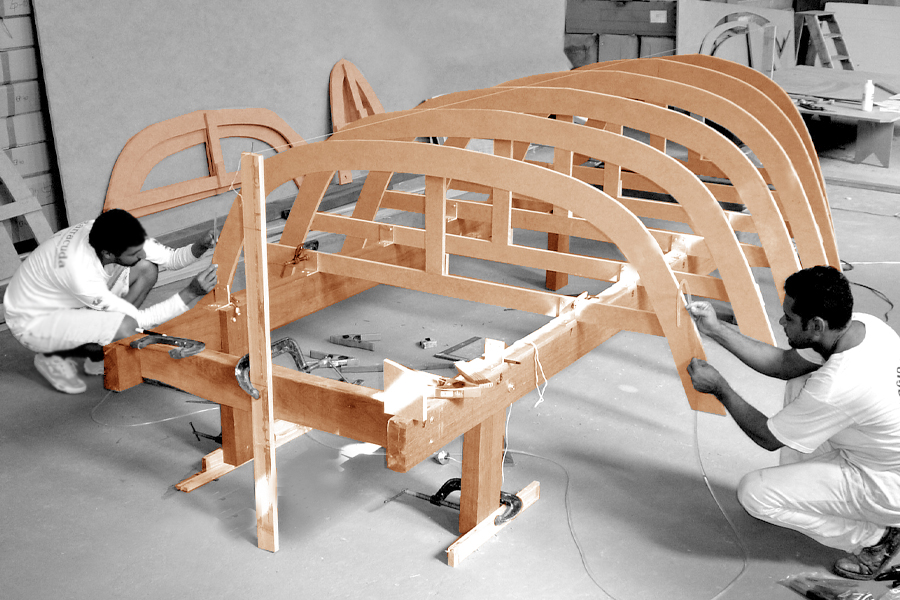
As espumas de PVC utilizadas para construção dos strips possuem densidades que variam entre 60 a 100 kg/m³ para a maioria dos projetos, com espessuras entre 10 e 50 mm, sendo que espessuras até 80 mm podem ser fornecidas caso seja necessário. As ripas de espuma devem ser cortadas com serra circular com uma boa lâmina e dispensam a usinagem de perfis macho e fêmea, como exigido paras as ripas de madeira, já que a colagem lateral é feita de topo, o que acaba reduzindo significativamente o trabalho de montagem.
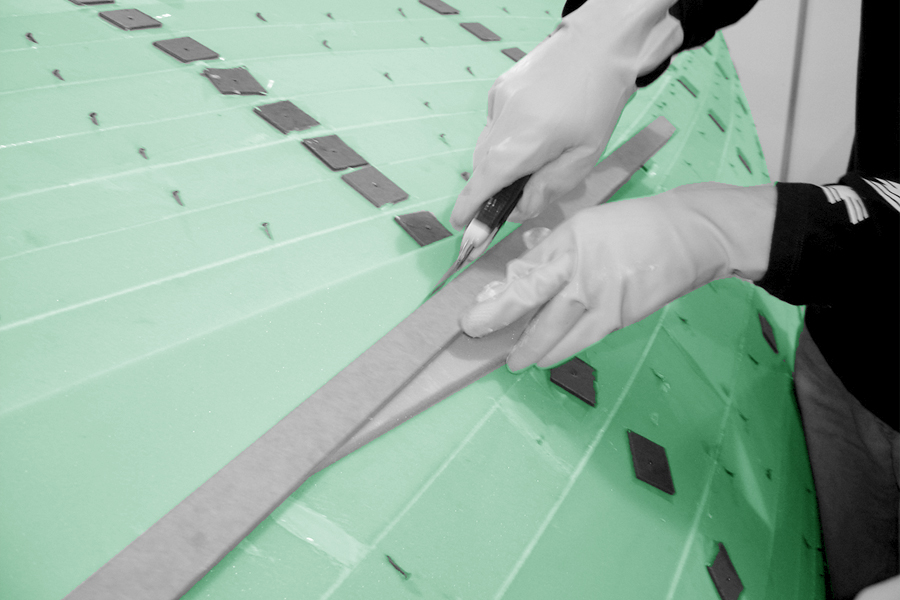
Inclusive, as ripas de madeira devem ter entre 20 e 25mm de largura e as de espuma podem variar entre 50 e 200mm, a depender do desenho das seções. A largura das ripas deve sempre ser maximizada de forma a diminuir o peso do adesivo, sendo inclusive possível que o construtor use placas com até 1200 mm de largura em barcos a motor com grandes superfícies planas.
As facilidades de montagem e colagem das ripas de PVC fazem com que seja possível diminuir consideravelmente o tempo de construção. Um barco pequeno de 25 pés pode ser montado em oito horas de trabalho, enquanto a construção em madeira levaria semana ou meses. Além disso, com o uso de madeira é obrigatório o uso de resina epoxy para a colagem das ripas e laminação da camada externa de fibras. A espuma PVC permite o uso de resina poliéster para laminação e colagem, o que diminui o custo e permite a construção de um laminado relativamente rígido.
O acabamento é outro aspecto onde o strip planking em PVC leva vantagem sobre o processo que utiliza madeira. Antes da laminação externa das camadas de fibra é necessário que a superfície do casco esteja perfeitamente aparelhada e por melhor que sejam as juntas de madeira, algum ajuste ainda será necessário. E lixar madeira é um processo muito mais trabalhoso do que lixar espuma rígida.
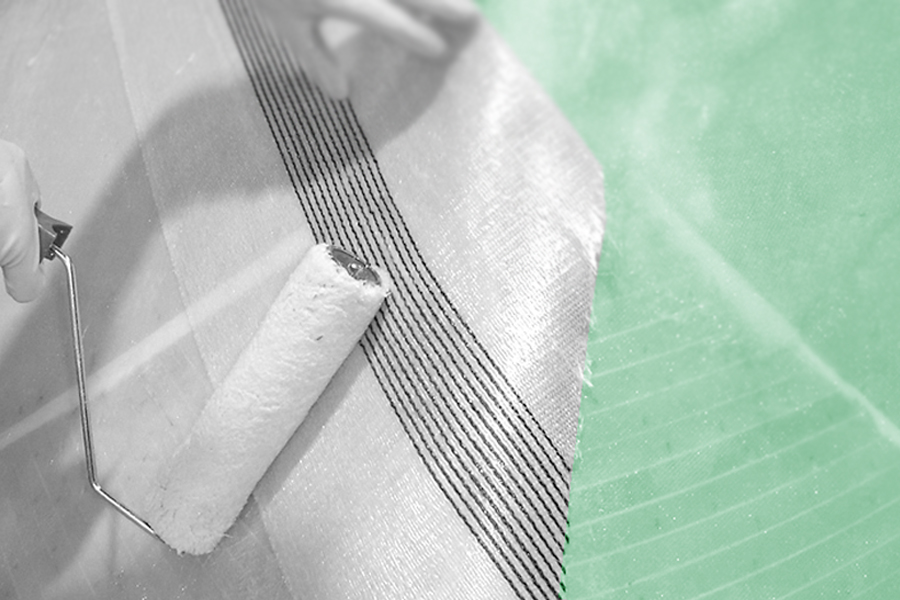
A seleção dos tecidos deve ser feita com base nos planos de construção criados pelo projetista, mantendo sempre as mesmas gramaturas e direções no caso de alguma adaptação. Tecidos biaxiais são sempre a melhor opção para construções one-off e têm a vantagem de permanecerem estáveis ao longo da laminação, diferente de tecidos woven roving, por exemplo, que criam superfícies irregulares. Em barcos muito grandes onde as camadas de fibra ultrapassam 3 kg/m², o construtor pode optar por utilizar um número maior de camadas de tecidos mais finos, que irão fornecer um acabamento quase perfeito.
Clique aqui para acessar Strip Planking em Espuma de PVC – Parte 2