O post da última semana descreveu os materiais consumíveis necessários para a laminação utilizando o processo de vacum bag. O processo de infusão a vácuo, apesar de com partilhar a maior parte dos materiais com o processo anterior, possui algumas diferenças.
As semelhanças, no entanto, estão no uso da tacky tape, bolsa de vácuo e peel ply. Os materiais utilizados são os mesmos e são selecionados da mesma maneira, sempre em função da temperatura de pico da cura exotérmica da resina.
As diferenças começam com o breather, que normalmente não é utilizado pois na infusão o gradiente de pressão tem o papel de inserir a resina no laminado, portanto não há excesso de resina a ser absorvido. Esse consumível aparece somente em infusões realizadas com duas bolsas, com o objetivo de distribuir a vazão de ar uniformemente por toda a superfície do molde.
O release film, ou filme perfurado, é utilizado apenas em dois casos. O primeiro é a infusão de laminados sólidos e o segundo é nas regiões onde são montadas as linhas de resina. Na laminação por vacum bag, o filme perfurado era responsável por ajudar na desmoldagem dos demais consumíveis e por controlar a resina que sairia do laminado.
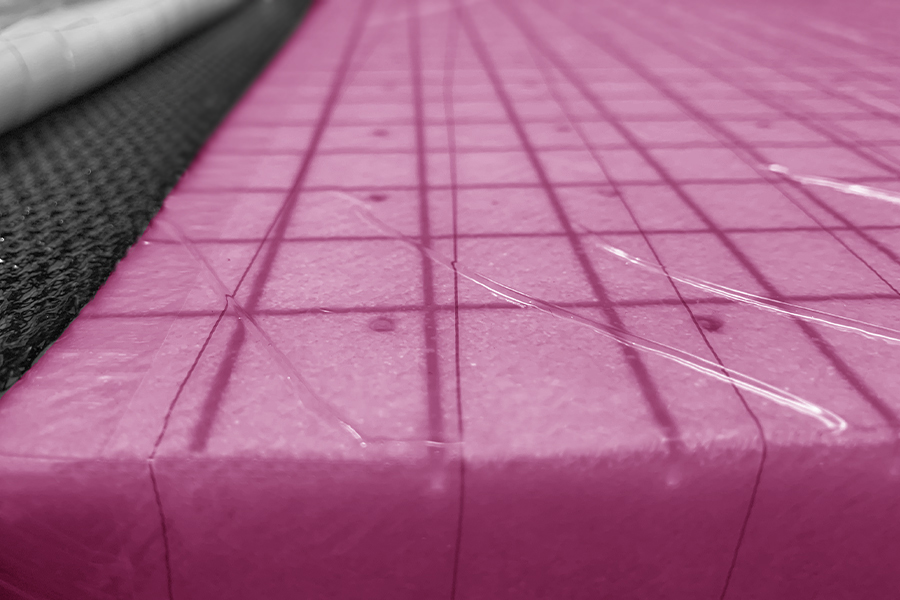
Na infusão, o filme perfurado ainda é um elemento facilitador da desmoldagem d os demais consumíveis, mas também é responsável por controlar a quantidade de resina que entra no laminado e, por essa razão, sua área aberta costuma ser maior e variar entre 1,0 e 1,5%.
Outro consumível utilizado na infusão é o flow media, chamado também de tela de infusão, que possui alta permeabilidade e distribui rapidamente a resina pela superfície do laminado. Isso facilita muito a impregnação de locais com baixa permeabilidade e torna possível a infusão de laminados sólidos.
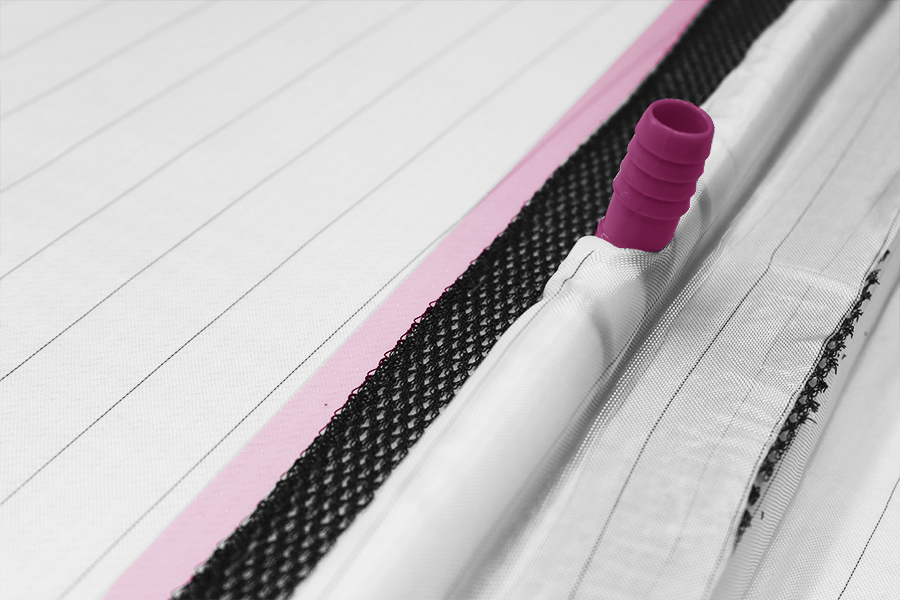
As linhas de entrada de resina são elementos essenciais para a realização de uma infusão de sucesso. A montagem dessa estrutura ocorre logo acima do peel ply e se inicia com o posicionamento de uma faixa de filme perfurado ao longo de todo o seu comprimento.
Acima do filme perfurado é aconselhável que se coloque uma faixa de flow media para que a resina se disperse facilmente ao longo de toda linha. Já a linha de resina em si é construída com um spiraduto envolvido em peel ply. O peel ply protegerá a bolsa de vácuo do contato com partes pontiagudas do spiraduto, evitando perfurações e vazamentos.
No centro da linha de resina, ou onde o plano de infusão determinar, deve ser posicionada uma conexão T que estará conectado à mangueira cristal que fará o transporte da resina. Essa mangueira deve ser preparada para ser submetida a pressão negativa, de modo que não colapse no momento em que a bomba de vácuo seja ligada. A fim de evitar vazamentos, a conexão da mangueira com o T deve ser isolada com tacky tape.
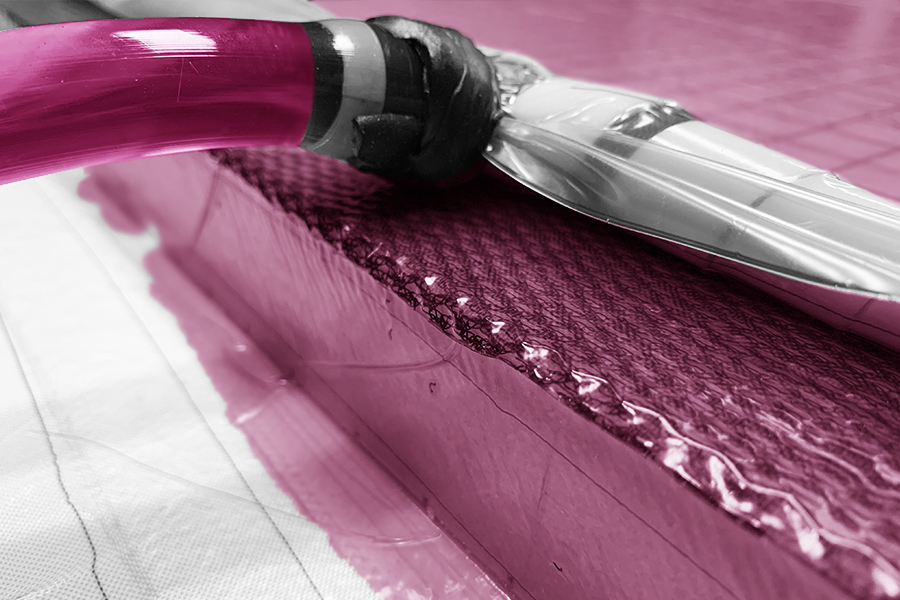
A saída de vácuo é construída de forma similar com spiraduto envolto em peel ply e uma conexão T ligada a uma mangueira cristal que é conectada à bomba de vácuo. Em geral, as linhas de vácuo são posicionadas em cima de um freio, ou uma área de baixa permeabilidade que serve para desacelerar o fluxo de resina e que normalmente será retirado da peça final. O freio evita que a resina entre na saída de vácuo e diminua a pressão aplicada à peça. Para facilitar a desmoldagem da linha, é comum que uma faixa de release film seja posicionada abaixo da linha de vácuo, apesar de não ser absolutamente essencial. Outro elemento importante para a infusão são os registros, que controlam o fluxo de resina e de ar dentro da peça e devem estar conectados às mangueiras.
O construtor deve ter em mente que o custo dos consumíveis representa apenas uma pequena fração do valor total dedicado a construção em composites e que a integridade da peça final depende da confiabilidade desses materiais durante o processo de infusão, então sua seleção deve ser feita de maneira criteriosa pensando nas temperaturas e esforços que eles irão suportar. Mais detalhes sobre o uso correto desses materiais podem ser vistos no vídeo sobre o Teste de Permeabilidade.