Desenvolver um conjunto de moldes para a produção de um determinado modelo de barco é uma tarefa complexa, e longa. A maioria dos grandes estaleiros tem sua própria divisão para fabricação de moldes, onde também são editados os manuais de construção, especificando informações e detalhes sobre como cada modelo deve ser construído. Isto inclui o passo a passo da construção, das camadas que vão ser laminadas, das proporções de fibra e resina e o peso final da estrutura. Um conjunto de informações desta podem necessitar de várias páginas e diagramas.
No caso de pequenas fábricas a fabricação dos modelos e dos moldes fica mesmo por conta de uma equipe de técnicos qualificados, encarregados das seções de modelagem. Contratar uma empresa para desenvolver moldes e protótipos ainda não é uma ideia costuma ser bem aceita no mercado náutico mas existe hoje um pequeno número de empresas que já prestam esse tipo de serviço.
Antes de mais nada, o fator econômico da fabricação dos moldes é importantíssimo. Geralmente, moldes são construídos quando se pretende fazer peças em série, aliando agilidade com eficiência no processo produtivo. No caso de embarcações, mais do que quatro ou cinco unidades já são economicamente suficiente para que construtores optem pela fabricação de um barco através de moldes. No caso dos barcos do tipo one-off ou protótipos, feito sob medida, gastar tempo e dinheiro com modelos acaba não compensando, uma vez que a qualidade de um barco construído nesse sistema pode ser tão boa ou mesmo muitas vezes superior aos fabricados em série.
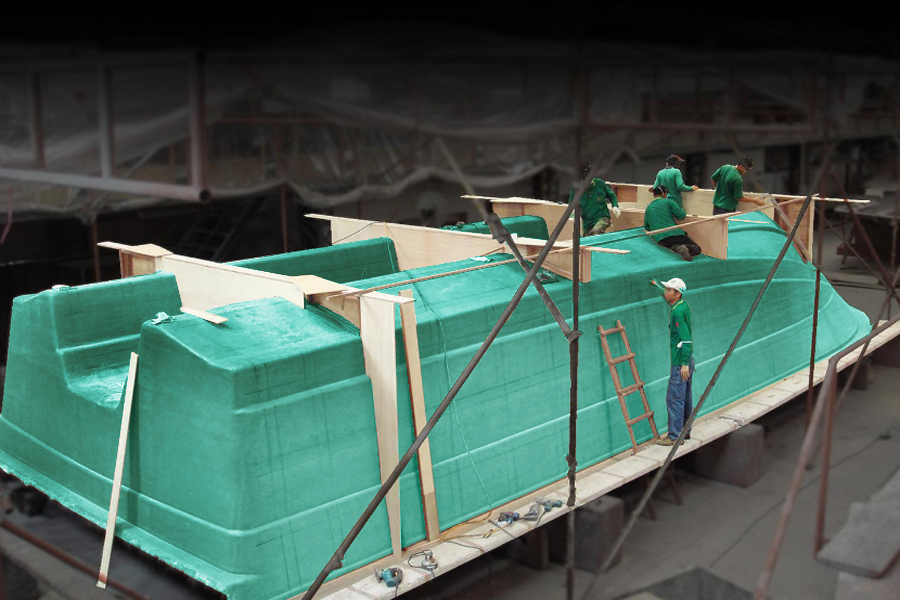
Decidindo-se finalmente pela fabricação de um conjunto de moldes, o construtor deve escolher que tipo de construção, materiais e sistemas de moldagem que melhor se adaptam à construção desse novo modelo. Outro fator importante é descobrir qual é a experiência anterior do construtor e o que ele espera do produto final que os moldes produzirão.
É sempre importante ter um conjunto de moldes perfeitos, mas por outro lado não faz sentido desenvolver um conjunto de alta qualidade com um custo elevado se o construtor está pensando em produzir um barco utilizando materiais de baixa qualidade, ou não tem experiência ou conhecimento para produzir embarcações de alto nível.
Geralmente um conjunto de moldes não se resume apenas as ferramentas do casco e convés, mas também devem estar incluídos contramoldes do interior, banheiros, peças do comando, fly bridge, targa, liners dos tetos, da cozinha, os sistemas de longarinas e das bases dos motores. O custo aproximado para desenvolver um conjunto completo, com quase vinte moldes deve levar em conta as alterações de projeto que são muito comuns e podem fazer com que os preços subam consideravelmente.
Outro detalhe é que o custo total não varia linearmente com o tamanho do barco. Se você pretende saber, por alto, quanto custará um molde, a conta mais rápida é calcular o valor do molde sendo de seis a oito vezes o valor final da peça acabada. Note que isto é apenas uma aproximação, já que o custo de um molde inclui também projeto, engenharia, detalhamento, design, modelagem, plug e, finalmente, o molde.
É um longo caminho a ser percorrido. Se custo indiretos forem incluídos nesta conta, o valor dos moldes pode chegar facilmente a dez vezes do valor da peça. É imprescindível uma boa planilha de custos, que inclua todo o processo produtivo dos moldes para determinar o preço, a mão de obra e o tempo gasto para se chegar ao produto final.