A rigidez de uma estrutura é o produto entre o módulo de elasticidade do material que a compõe e o momento de inércia da seção transversal. O momento de inércia, por sua vez, aumenta exponencialmente em função da espessura t de um laminado.
A melhor maneira de determinar qualquer propriedade de materiais compostos é experimentalmente, ou até mesmo na prática nas condições reais de fabricação. No entanto, existem algumas ferramentas que podem auxiliar construtores e projetistas a estimarem essas propriedades e realizarem ensaios mais assertivos, já na janela mais adequada de experimentação.
Uma dessas ferramentas é a Equação 1, que permite estimar a espessura t de um laminado sólido com base no número de camadas n do tecido de gramatura Aw utilizado. Para utilizá-la, é importante também saber a densidade ρf do filamento utilizado e a fração volumétrica vf de fibra no laminado.
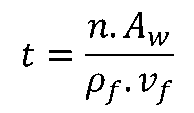
O número de camadas e a gramatura do tecido utilizado são variáveis fáceis de serem determinadas e normalmente são apresentadas no plano de laminação da estrutura. A densidade do filamento varia de acordo com o material utilizado, sendo aproximadamente 2,7 g/cm³ para fibras de vidro e 1,65 g/cm³ para fibras de carbono. Essa informação deve ser sempre confirmada com o fornecedor do material.
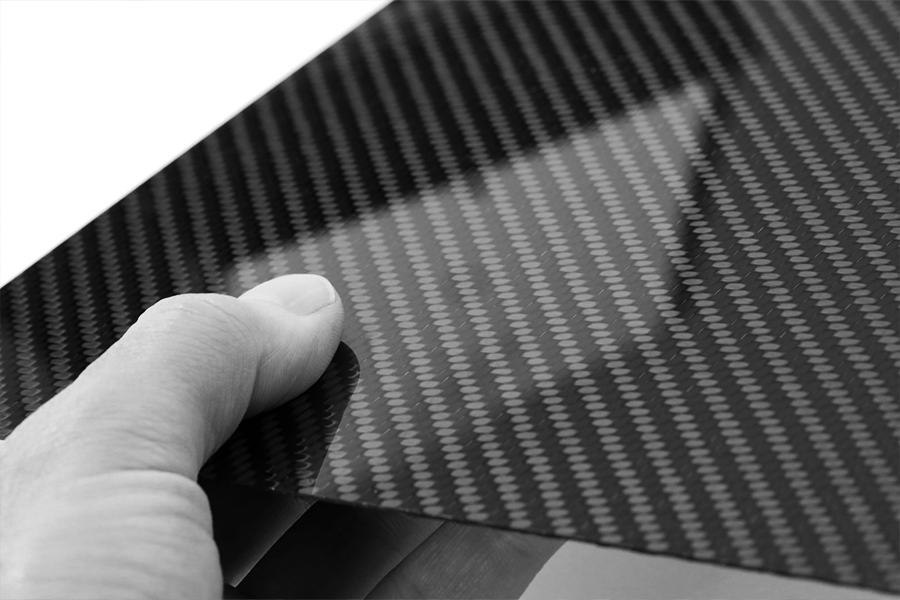
A fração volumétrica de fibra em um laminado é um número entre 0 e 1 que indica qual a porcentagem do espaço que a fibra ocupa em relação ao volume total do laminado. Não é fácil obter esse número na prática como é obter o teor de fibra, também chamado de fração mássica de fibra, que é simplesmente o peso de fibra divido pelo peso total do laminado.
A Equação 2 permite converter a fração mássica de fibra em fração volumétrica informando as densidades da fibra ρf e da matriz ρm utilizadas para construção do laminado sólido.
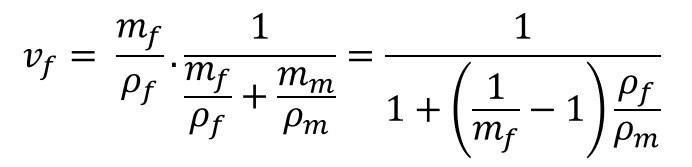
O teor de fibra depende principalmente do processo de fabricação utilizado e varia de acordo com o indicado no Gráfico 1. Métodos como spray-up e laminação manual apresentarão uma variação nesses valores em função do operador que está realizando o processo, mas processos mais sofisticados como a infusão e prepregs são capazes de obter teores mais alto e variabilidades menores.
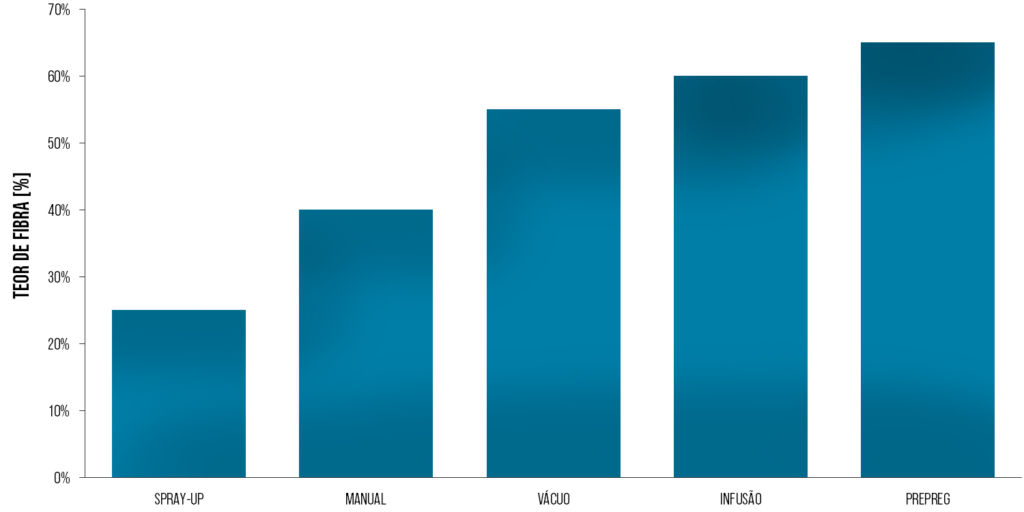
Assim como outras diversas propriedades mecânicas e físicas dos materiais compostos, é possível estimar a espessura de laminados sólidos em função das propriedades dos constituintes e parâmetros do processo de fabricação. É possível encontrar mais informações e uma discussão mais profundo desses parâmetros no livro Processo de Infusão a Vácuo em Composites.