Muitos projetistas se concentram em produzir planos de construção, indicando detalhadamente a sequência e direção das camadas de tecido, espessuras e densidades de núcleos, mas negligenciam o detalhamento de pontos críticos da construção de composites.
No entanto, após acertar o processo produtivo e o plano de laminação, os detalhes das uniões entre os elementos estruturais são pontos que podem determinar a segurança da embarcação e, se feitos da maneira correta, podem ajudar a reduzir seu peso.
Essa série de posts será dedicada a detalhar alguns desses pontos críticos e apresentar quais são as melhores soluções para construí-los. Apesar de retratarem a união de elementos náuticos, os exemplos são genéricos e podem ser aplicados em qualquer tipo de construção em composites. O primeiro deles se trata da montagem entre casco e convés.
Existem diversas opções de como esse procedimento pode ser realizado, dependendo do tipo de laminado utilizado, moldes e acabamento final que o construtor espera alcançar. Em geral, barcos produzidos em série tendem a utilizar fixadores de metais combinados com laminações internas.
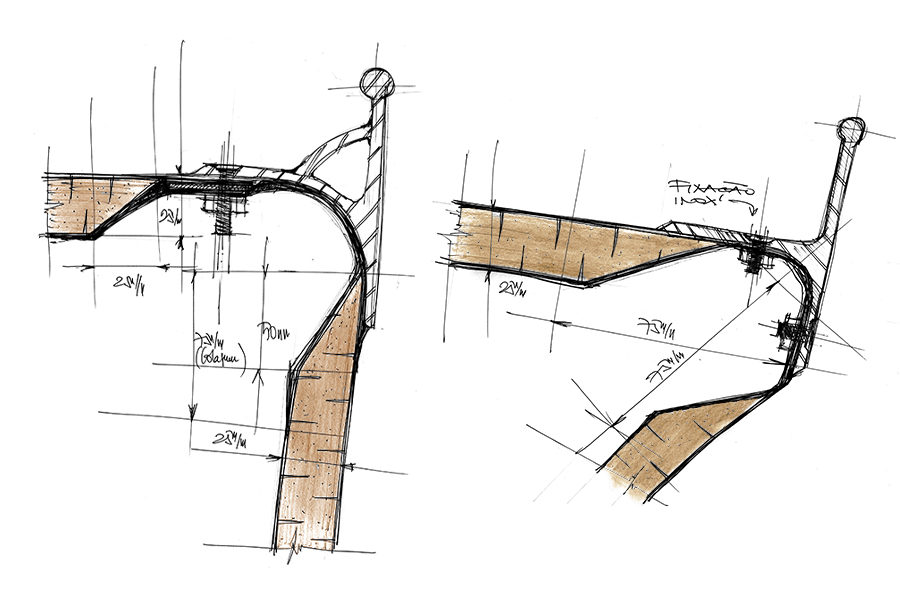
A figura acima mostra duas soluções de fixação de casco e convés fabricados com laminados sandwich. À esquerda, a fixação é feita através de adesivo estrutural no plano do convés através de um rebaixo, e finalmente o trilho de borda é fixado com parafusos passantes. A parte interna da junção pode ou não ser laminada dependendo do grau de acessibilidade da junção.
A ilustração à direita mostra uma variação do exemplo anterior onde se utiliza o rebaixo na face superior do costado e o trilho de borda é montado com dupla fixação metálica. A terminação da espuma deve ser o mais próxima possível da linha de montagem para reduzir o efeito da mudança brusca de inércia entre o laminado sandwich e o laminado sólido.
É importante notar que a espuma PVC não possui resistência à compressão suficiente para receber fixadores, portanto as ferragens devem ser unidas aos painéis com adesivos estruturais e os parafusos devem ser posicionados diretamente nas partes metálicas ou em porções sólidas do laminado. Quando é necessário que sejam utilizados diretamente sobre o painel, o construtor deve realizar um insert de espuma poliéster de alta densidade.
A próxima opção à disposição dos construtores é ilustrada na figura abaixo e é bastante utilizada em barcos pequenos de produção seriada com difícil acesso pela parte interna utiliza o rebaixo na linha do casco. A montagem é feita com adesivo estrutural e depois terminada com trilho de alumínio ou aço, fixada por parafusos com acabamento metálico ou plástico e selante a base de poliuretano.
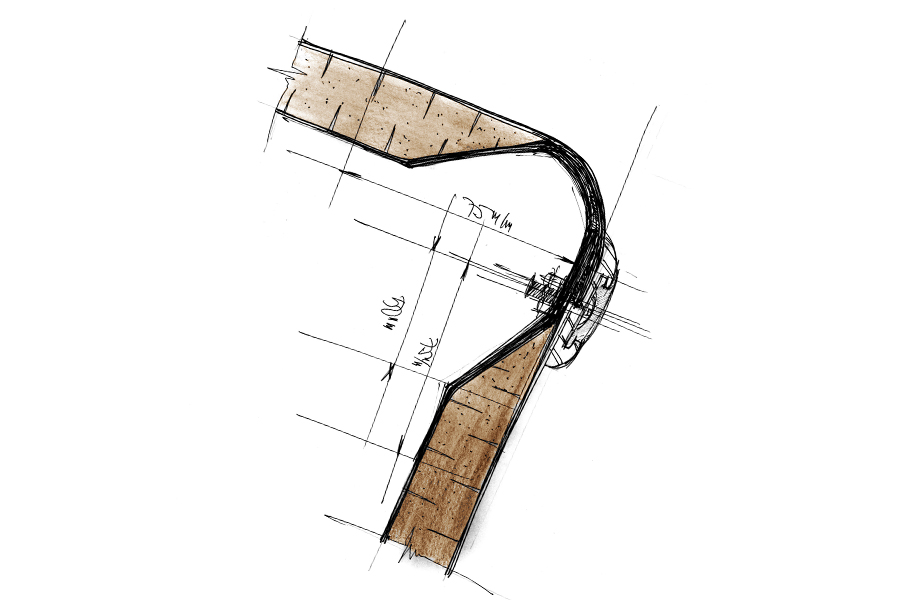
Existem ainda opções que utilizam somente adesivo estrutural, sem a presença de fixações metálicas. O primeiro detalhe mostra a colagem vertical simples com adesivo epoxy ou metacrilato, enquanto o segundo mostra a colagem com adesivo no plano horizontal com laminação interna.
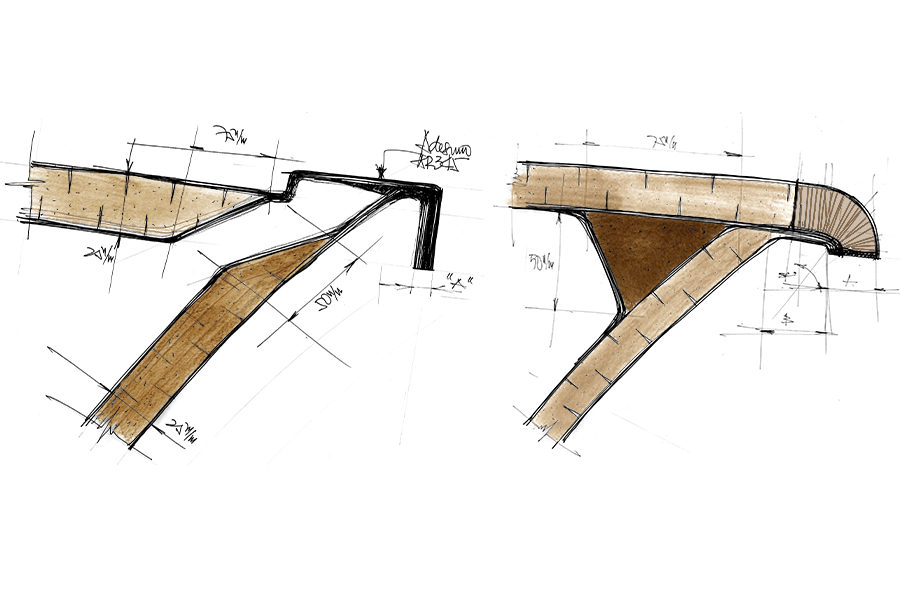
Essas são algumas das opções disponíveis para execução desse tipo de procedimento de união, que prioriza a segurança e eficiência estrutural da construção com laminados sandwich. Outras estratégias estão presentes no livro Métodos Avançados de Construção em Composites.