O último post da série sobre o processo de Strip Planking em Espuma PVC, método desenvolvido pelo departamento de engenharia da Barracuda Advanced Composites, abordará o posicionamento dos strips e a laminação do casco. Depois de passar uma visão geral do método, o post anterior abordou a confecção e posicionamento das cavernas sob o picadeiro. A partir de agora, com a montagem da estrutura da embarcação realmente, fica evidente o ganho de produtividade que o método em PVC entrega em relação ao método tradicional em madeira.
Após o ajuste as cavernas, é necessário que seja instalado um virote longitudinal de madeira marcando a linha de borda da embarcação. Esse virote deve ser livre de empenos, ter a mesma espessura das chapas de espuma e apresentar cortes perfeitamente transversais espaçados entre 200 e 400 mm, sendo fixado nas cavernas com pregos ou parafusos. É nele que a primeira ripa de espuma será fixada com parafusos e a partir dela que a construção se desenvolve.
As ripas de espuma devem ser cortadas em uma serra circular com as larguras determinadas pelo projetista. Como as placas de PVC têm no máximo 2400 mm de comprimento, muitas vezes será necessário que se façam emendas longitudinais nas ripas. Já no post sobre a visão geral, se destacou que uma das vantagens do Strip Planking em PVC era que as ripas podem ser coladas de topo com resina poliéster, proporcionando uma redução de custo e tempo de fabricação em relação aos strips de madeira que devem ser colados com adesivo epoxy e encaixados a partir de perfis machos e fêmeas que precisam ser usinados. As emendas longitudinais na madeira devem ser feitas em chanfro de pelo menos 8:1 o que é realmente trabalhoso.
Além do adesivo de poliéster, as extremidades dos strips devem ser fixadas com o auxílio de pregos costurados de forma oblíqua, evitando o deslocamento após a colagem. Depois da preparação das ripas, é necessário aplicar desmoldante sobre as cavernas. Uma solução simples e rápida para restar etapa é simplesmente cobrir o topo das cavernas com uma fita plástica transparente.
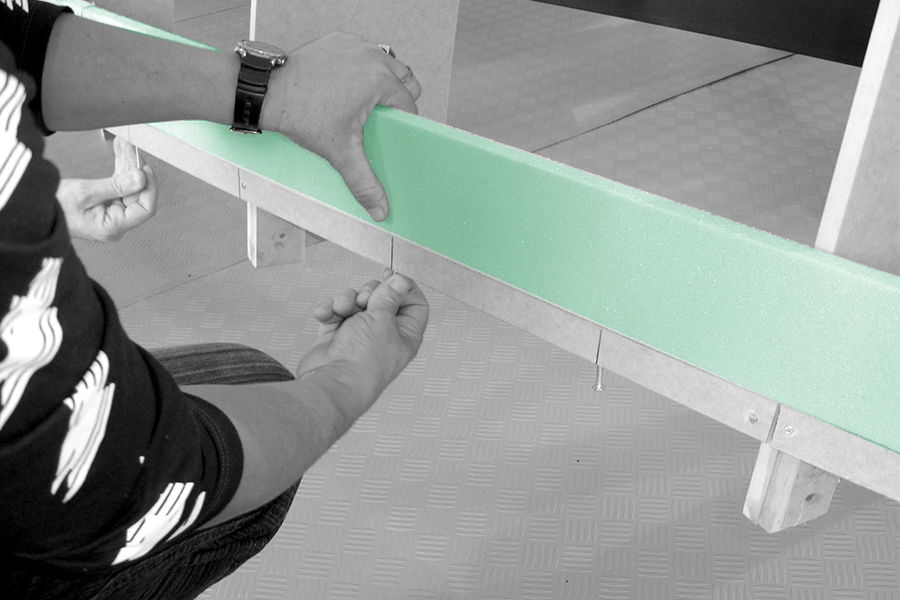
É chegada então a hora de posicionar o primeiro strip no virote de madeira que indica a borda da embarcação. Após o alinhamento da ripa na popa do barco com uma sobra de cerca de 200 mm, deve-se conformar a ripa ao longo das cavernas e verificar que na proa também há uma sobra de 200 mm. Feito isso, é preciso fixar a ripa de espuma com parafusos auto-atarraxantes, capazes de abrir progressivamente uma rosca em espumas com densidades entre 60 e 80 kg/m³.
Depois da ripa estar fixada pelos parafusos, ela deve ser presa à caverna com pregos, que devem ser montados por meio de um pequeno bloco de madeira compensada de 4 mm de espessura, e 40×40 mm de área. Após esta etapa, a segunda ripa já pode ser posicionada com o uso de adesivo, utilizando uma regra geral de que cada metro de ripa de PVC com 20 mm deve receber entre 60 e 80 gramas de adesivo.
Com duas pessoas trabalhando, é possível catalisar massa para colagem de três ou quatro ripas de cada vez, utilizando a quantidade que sobrar para realizar o rejuntamento das ripas. Depois da colagem de uma ripa, é necessário sempre realizar a fixação nas cavernas com pregos, seguida da limpeza do excesso de massa entre as ripas e inserção de pregos para a junção. Esses pregos devem ter entre 2 e 3 mm de diâmetro, comprimento de 40 mm e um espaçamento de 200 mm entre eles.
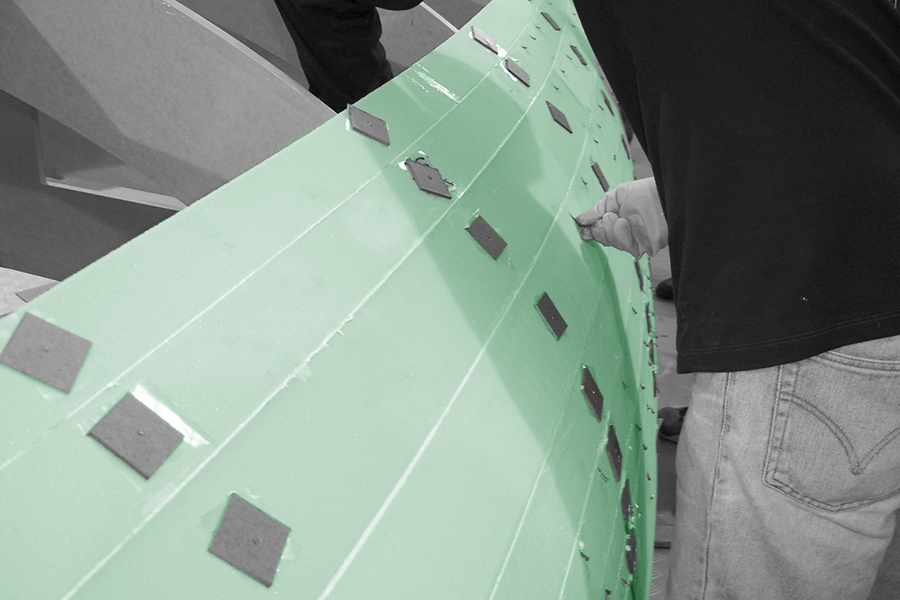
É comum que as primeiras ripas do costado sejam fáceis de serem posicionadas, mas chegando perto da intersecção do fundo com o costado, a geometria das ripas começa a mudar e o construtor pode optar por continuar o trabalho reduzindo o comprimento das ripas ou pode iniciar a montagem das ripas pela linha de centro do barco, possibilitando o início de duas frentes de trabalho.
Concluído o chapeamento do costado, a ripas vindas da linha de centro vão começar a terminar em escala sobre a última ripa do costado. Neste ponto o construtor deve ajustar a próxima ripa sem o adesivo. Colocar a ripa faceando a ripa inferior e com o auxílio e uma outra ripa como régua marcar o ângulo de corte e realizá-lo utilizando uma faca ou estilete para um corte limpo e preciso.
O fechamento da proa é uma das partes mais difíceis da construção em strip planking, já que o perfil da roda deve ser sempre ajustado para acomodar as mudanças dos ângulos e a posição das cavernas deve ser precisa para não criar ondulações no casco. Na maioria dos casos, é aconselhável adicionar cavernas intermediárias para facilitar a colocação das ripas. Se o espaçamento das cavernas for de 700 mm, é interessante diminuí-lo para 350 mm nas primeiras duas cavernas para poder proporcionar uma montagem suave e garantir as linhas de proa do barco.

Assim que o Strip Planking estiver concluído, é hora de retirar com cuidado os pregos de costura e os pregos e arruelas do contraplacado, aparar as ripas da última baliza de ré e preparar uma massa para calafetar todas as pequenas juntas entre as ripas que ainda podem estar abertas e as regiões em que os pregos podem ter deixados marcas nas espumas. Quando esse processo estiver concluído, a superfície de espuma deve ser lixada e mais uma vantagem do uso de PVC fica evidente nesse processo.
É muito mais rápido e fácil lixar uma superfície de espuma com tacos de madeira com lixa do que realizar o mesmo processo nos strips de madeira. Deve-se começar com uma lixa de ferro grão 40 e prosseguir o acerto fino no costado e na roda de proa com lixa grão 60 e 80. É muito importante que o lixamento seja feito de forma primorosa para que o acabamento final da embarcação seja de ótima qualidade e evite que muita massa seja aplicada de pois da laminação.
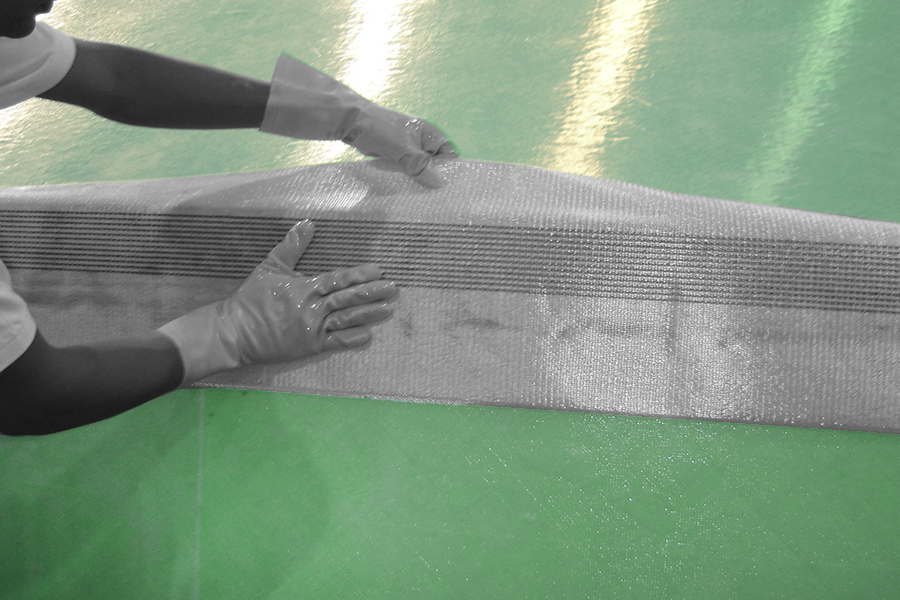
Após o lixamento, é possível começar o preparo para a laminação que se inicia com o pré-corte e pesagem dos tecidos, sempre se certificando de que os overlaps não ultrapassem 50 mm e seguindo atentamente as instruções do plano de laminação. Sabendo o peso total de fibras que será utilizado em conjunto com o teor de fibra de vidro adequado, o construtor é capaz de calcular a quantidade de resina a ser utilizada em uma laminação manual, incluindo uma taxa de 5% para eventuais perdas.
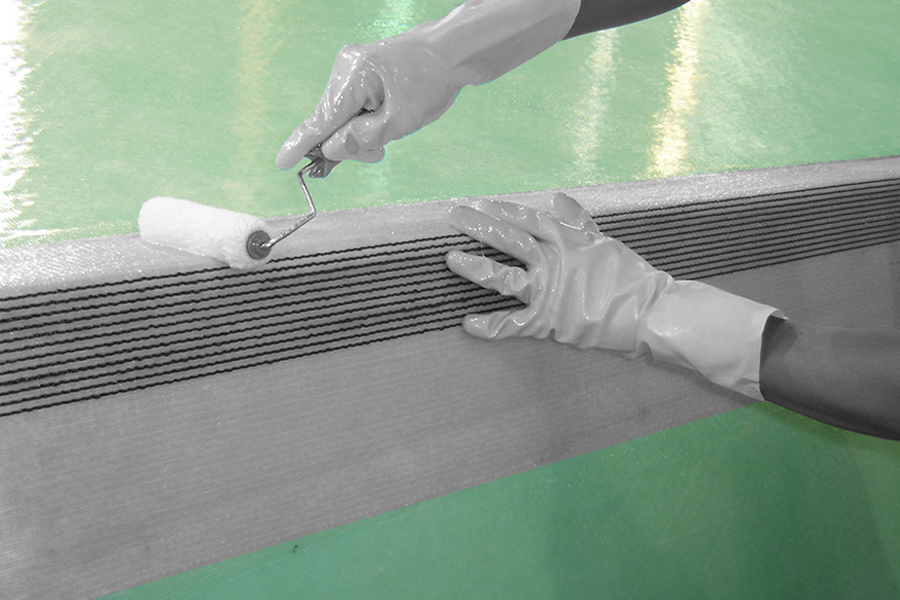
Para garantir que a superfície externa esteja preparada para o acabamento, é possível inserir uma última camada de laminação de peel ply, opcional para barcos construídos em resinas poliéster, mas mandatório para construção em epoxy.

Após a cura da laminação externa, é necessário virar o casco e laminar a parte interna para que os painéis sandwich sejam consolidados. O processo todo de construção de um casco por meio do Strip Planking em espuma de PVC pode ser executado em um período de algumas semanas, representando um ganho em custo e produtividade muito grande em relação ao Strip Planking de madeira, isso sem contar que o casco será mais leve e muito mais durável. No final este tipo de construção é mais rápida, mais forte, mais durável, mais leve e mais econômica!
Clique aqui para acessar Strip Planking em Espuma de PVC – Parte 2
Clique aqui para acessar Strip Planking em Espuma de PVC – Parte 1
Lucas Eduardo disse:
Qual a grande vantagem do uso da resina poliéster sobre a resina epoxy já que em geral a epoxy garante maior poder de adesão e melhores propriedades mecânicas?
Barracuda Composites disse:
Olá, Lucas
Realmente as resinas epoxy são excelentes e trazem muita vantagens para projetos que precisam dessa alta adesão, mas isso vem com um alto custo. Quando se pretende fazer um laminado com fibra de carbono, por exemplo, faz sentido investir em uma resina que seja capaz de transferir os esforços da melhor forma possível para os reforços. Mas um bom projetista deve estar preocupado com a eficiência, que significa entregar rigidez e resistência o suficiente com o menor custo possível sem comprometer a qualidade. Como até já foi discutido nos posts anteriores da série sobre Strip Planking com Espuma PVC, a resina poliéster consegue entregar a resistência que a embarcação precisa por um custo muito menor do que a epoxy.
Eduardo Ramos disse:
Como é vendida, ou seja, quais as dimensões da placa de pvc?
Barracuda Composites disse:
Olá, Eduardo
Placas de PVC são disponíveis com uma grande variedade de dimensões. As espessuras podem ser selecionadas entre 10 e 50 mm, sendo que é possível chegar até 80 mm. As densidades variam entre 45 e 250 kg/m³, sendo comum construir embarcações de pequeno porte com espumas de até 130 kg/m³. O comprimento máximo das placas é de 2.400 mm, mas alguns fornecedores podem entregar as placas em dimensões menores em função da necessidade do cliente. Lembrando que, apesar de o comprimento máximo ser de 2400 mm, você pode colar as ripas com massa poliéster para alcançar o comprimento que for necessário e ainda infundir diversas placas de PVC para produzir um painel do tamanho que desejar. Você pode encontrar mais detalhes sobre construção com espumas de PVC nesse post do nosso blog.
Ricardo Ramalho disse:
Como fica a colagem das anteparas de espuma do casco de espuma? Primeiro lamina o casco e depois cola as anteparas? Daí tem que laminar as anteparas, certo? Algum reforço é necessário nos pontos de colagem?
Barracuda Composites disse:
Olá, Ricardo
Sim. Você precisa laminar a face interna do casco antes de posicionar a antepara, também construída em sandwich, na posição correta. Para fixá-la de forma adequada e facilitar a laminação posterior é possível fazer um filete com massa poliéster com microesferas. Então é necessário laminar uma camada de tecido biaxial de fibra de vidro (XM1808 é uma boa opção) em cada um dos lados. O comprimento dessa camada varia com o comprimento do barco, mas em geral 200 mm é o suficiente. Mais detalhes sobre a montagem e colagem das anteparas podem ser encontrados no último capítulo do livro Métodos Avançados de Construção em Composites.
Cristiano Martins Bittencourt disse:
É possivel construir cascos de multichine com este material? Quais as adaptações necessárias pra usar espuma de PVC quando o projeto é feito pra compensado naval?
Barracuda Composites disse:
Olá, Cristiano
Sim! A construção em strip planking com espumas PVC é uma ótima opção para construção de cascos multichine, garantindo rapidez na fabricação e confiabilidade estrutural. Você vai precisar fazer uma seleção nova de materiais onde será possível agora utilizar resina poliéster, que vai baixar o custo de fabricação. Além disso, não há dúvidas que a embarcação final será mais leve, já que o PVC tem maior eficiência na resistência e rigidez em comparação ao compensado naval.
Maicon disse:
Olá,
lendo o post acima, fiquei com uma dúvida sobre o tipo de resina a ser utilizada. Como vocẽs sugerem o uso de resina de poliéster, uma questão me veio a mente é o risco do surgimento de osmose (que parece ser mais comum em cascos feitos com esse tipo de resina). Qual seria a melhor solução para isso? Fazer uma última camada externa com base em resina epoxy para funcionar como uma barreira?
Barracuda Composites disse:
Oi Maicon!
As resina poliéster que mais sofrem com a alta absorção de água são as formadas a partir de ácido saturado ortoftálico e isso é particularmente crítico quando se utiliza núcleos de madeira, que apodrecem em contato com umidade. Espumas PVC já não sofrem desse problema porque células fechadas e não absorvem água, o que já possibilita o uso de resinas poliéster. Além disso, é muito comum hoje em dia que os construtores utilizem resinas poliéster isoftálicas, que já são muito mais resistentes à entrada de água.
Fernando Raposo disse:
Olá.
Pretendo construir um veleiro Samoa 34 MK2 do Cabinho/Luís Golveia. O projeto pode ser executado em madeira epóxi ou Divinicell poliéster. Prefiro a construção em espuma porém, como eng.. civil, não possuo nenhuma experiência no assunto. A princípio seria em madeira pela minha disponibilidade de ferramental e boa habilidade com este material. Tenho algumas duvidas:
1. Existe algum curso de fabricação presencial para melhor adaptação ao uso das espumas como mostrado nas fotos?
2. A Barracuda disponibiliza seu depto de engenharia para “validar” ou melhorar o projeto em função dos materiais oferecidos por sua empresa?
3. Neste projeto devemos consumir uns 130m2 de H80 com 20mm e uns 350kg de resina mais tecidos. Há possibilidade da compra total com pagamento parcelado?
4. Como sou de Sjcampos, SP e Barracuda no RJ, o valor será diferente em PJ.
Antecipadamente obrigado e parabéns a equipe.
Sds
Barracuda Composites disse:
Olá, Fernando
No momento, não estamos realizando cursos presenciais. Qualquer novidade sobre isso, estaremos divulgando nas nossas redes sociais.
Durante o processo de aquisição dos materiais, podemos discutir quais são as melhores opções dentro da gama de materiais que oferecemos, assim como quais são as melhores opções de processo de fabricação que você pode utilizar.
Fornecemos a espuma H80 e uma variedade de tecidos de fibra de vidro na loja online, a e-composites, que permite o parcelamento da compra.
José Epifanio disse:
Bom dia! A espuma de PVC que utilizaram para esse Strip Planking é a mesma PET ARMACELL GR80 GSP vendida no site? Ela no site é vendida no tamanho 80×60 cm. Onde está no site a placa de 2400mm?
Barracuda Composites disse:
Olá, José
Não. A espuma de PVC que normalmente é utilizada para construção em strip planking está identificada no site como Divinycell. A densidade e espessura das placas de espuma vai depender do projeto estrutural da embarcação. A espuma PET é fabricada com outro material e possui propriedades mecânicas diferentes.
Pelo site da e-composites, as placas de espuma são vendidas por 80×60 cm, o que não prejudica a fabricação de painéis maiores, já que as espumas podem ser posicionadas lado a lado e serão unidades sem nenhum tipo de prejuízo estrutural durante a laminação das faces de fibra.
Fernando disse:
Boa tarde, tenho uma dúvida em relação à laminação do casco. Ele tem que ser laminado todo de uma vez Todas as camadas de fibra? Caso não seja possível laminar todas as camadas de uma só vez, como proceder? Obrigado.
Barracuda Composites disse:
Olá, Fernando
Se você precisa fabricar um laminado sólido com espessura maior que 4 mm por laminação manual, o processo deve ser realizado em etapas para garantir que não haja pontos de alta concentração de calor durante a cura da resina.
Para garantir que a superfície do laminado esteja pronta para receber mais camadas, você deve aplicar uma camada de peel ply depois de terminar a laminação de cada etapa. O peel ply deve ser retirado apenas antes da próxima etapa de fabricação, após a cura completa da resina.
Isaias Freitas da Silva disse:
Tenho interesse em construir uma embarcação pesqueira de 22m de comprimento. Podem me passar o orçamento detalhado?
Barracuda Composites disse:
Oi Isaias.
Primeiro você precisa de um projeto e informar qual o método de construção que você pretente utilizar. Esta embarcação é para pesca comercial ou pesca esportiva?
Martin disse:
Muito obrigado pelo blog, informações muito boas.
desculpe pelo meu português, mas eu sou do Uruguai
pode ser laminado com Infusão a Vácuo o apenas manual
Barracuda Composites disse:
Olá Martin!
A laminação sobre o strip planking deve ser manual, pois você não vai conseguir selar a parte interna do barco e, logo, não conseguirá dar pressão de vácuo suficiente.
Anderson Rios disse:
Olá!
Onde podemos adquirir strip de pvc como esses das fotos?
Barracuda Composites disse:
Sim. Podemos fornecer a espuma ja precortada em tiras de 25-20-40-50mm
Quantos m2 voce vai precisar?
Qual a espessura da espuma e qual a largura dos strips?